Press Releases
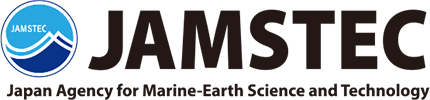
JAMSTEC
AGC Inc.
World-First Success in Nearly Perfect Reproduction of the Fracture Process of Chemically Strengthened Glass Using a New Numerical Analysis Method
— Application in Predicting Earthquake Fault Behavior
1. Key points
- ◆
- The dynamic fracture process in a chemically strengthened glass has been successfully simulated for the first time.
- ◆
- The numerical analysis method presented in this research is a novel theoretical development, which enables precise evaluation of the dynamic fracture process in a residual stress field.
- ◆
- This research showed the existence of fracture phenomena with their fate predetermined at the start. Our theoretical and numerical analysis result unravels the universal physics that governs the process: the accumulated strain energy is released by fracture and has the potential to elucidate the behavior of earthquake faults.
2. Overview
Researcher Sayako Hirobe and her colleagues at the Center for Mathematical Science and Advanced Technology (MAT), Research Institute for Value-Added-Information Generation (VAiG), Japan Agency for Marine-Earth Science and Technology (JAMSTEC) have succeeded in the world-first nearly perfect reproduction of the process of shattering chemically strengthened glass sheet by numerical analysis of dynamic fracture in a residual stress field.
Glass is a material that is resistant to compressive forces and weak against tensile forces. Chemically strengthened glass is glass that has undergone ion exchange to generate strong compressive stress on its surface, which makes it much stronger than ordinary glass. Nevertheless, tensile stress accumulates inside a chemically strengthened glass, and if a scratch on the surface reaches a region of tensile stress inside, the glass fractures in an instant. While it is believed that elucidating the physics of this fracturing process will lead to the development of stronger materials, it has been difficult to analyze the process because the crack propagates at high speed and branches repeatedly in unexpected directions.
As a result of numerical analysis of dynamic fracture propagation using a newly developed theoretical method for analyzing such propagation in a residual stress field, the research group has made a worldwide breakthrough by successfully completing a nearly perfect reproduction of the fracture process of chemically strengthened glass sheet. The numerical analysis reproduced well the various fracture propagation processes according to the level of residual stress stored in the chemically strengthened glass sheet (Figure 1). In addition, the study depicted an instantaneous fracture propagation process at a nanosecond-scale time resolution (Figure 2).
Our result reproduces the phenomenon that is universally observed in the process of releasing accumulated strain energy by fracture and is expected to help elucidate and predict earthquake fault behavior in the future.
The work has been accepted as a joint submission to Physical Review Letters and Physical Review E, and is scheduled for publication on August 4, 2021(Japan time).
This research was partially supported by JSPS research grant JP20K14812.
Mathematical model and numerical analysis method for dynamic fracture in a residual stress field (Physical Review E)
- JAMSTEC
- AGC Inc.
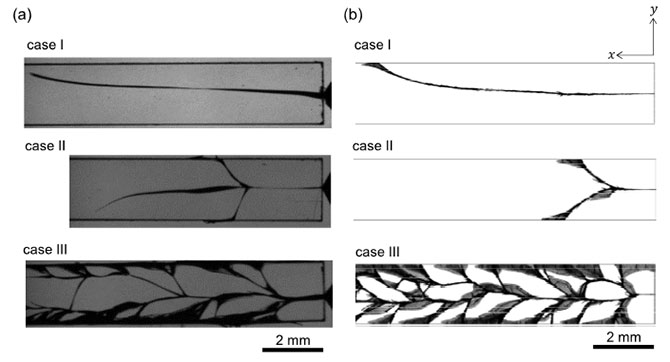
Figure 1. Fracture of chemically strengthened glass sheet (a) Experiment (b) Numerical analysis.
- Case I:
- Residual stress level: low
- Case II:
- Residual stress level: medium
- Case III:
- Residual stress level: high
The fracture is initiated by tapping lightly on the center of the rightmost edge of the glass plate to create a small chip, after which a crack develops without external force.
The higher the residual stress level, the more violently the crack branches out.
In the numerical analysis, a very fine analysis mesh is used to divide a 30 mm wide, 2 mm high, and 0.7 mm thick glass plate into approximately 4,000 sections in the width, 260 sections in the height, and 100 sections in the thickness directions.
The curving of the fracture surface in the thickness direction observed in the experiments (especially Case III) is excellently reproduced by the numerical analysis.
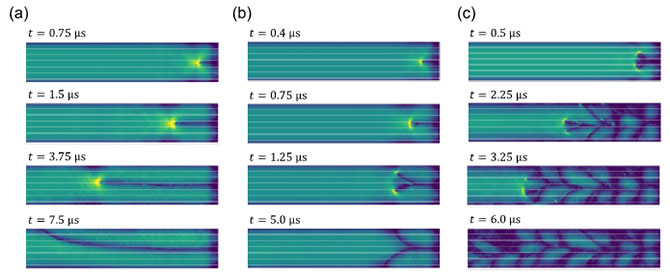
Figure 2. Numerical analysis results for stress waves at the center of the plate thickness during fracture
- (a)
- Residual stress level: low
- (b)
- Residual stress level: medium
- (c)
- Residual stress level: high
Physical quantities that cannot be photographed in experiments are visualized by numerical analysis.
In addition to the stress waves during fracture, the image at the final snapshot shows the distribution of residual stress that remains in the fragments without having been released after the fracture.
Contacts
- (For this study)
- Sayako Hirobe, Researcher, Research Institute for Value-AddedInformation Generation(VAiG), Center for Mathematical Science and Advanced Technology (MAT), Computational Science and Engineering Group, JAMSTEC
- (For press release)
- Public Relations Section, Marine Science and Technology Strategy Department, JAMSTEC