Like Threading a Needle from Atop a Building
JFAST will involve boring two 1,000m-deep holes, with diameters of 27 cm, on the ocean floor 7,000m below the sea surface. Temperature will be monitored in the first borehole, and both temperature and pressure will be measured in the second.
Priority will be given to the first borehole, which will collect detailed data using 55 heat sensors. The second borehole will employ different methods to measure heat to ensure the accuracy of the data collected, and will simultaneously collect data on pressure. “Traces of tectonic activity can also be gleaned from changes in formation fluid pressure,” Kyo explains. “In other words, by monitoring pressure, we can ascertain fluid behavior, and combining this with heat measurements will give us a more profound understanding of movement of Earth crust.”
Being able to collect data from all the sensors would be ideal, but before this is possible, the monitoring equipment must first be installed as planned. This requires overcoming major technical hurdles, however, as it is planned to drill down into 7,000m below the seafloor, rather than just 2,000m, as was the case for the NanTroSEIZE. The equipment will be installed using pipes measuring 14cm in diameter.
These daunting challenges can be better grasped by conceptualizing the task on a scale of 100 to 1. Imagine lowering a long piece of thread with a diameter of 1mm from the top of a 70m building—equivalent to an 18-story structure if each floor is 4m high—into a hole in the ground measuring just 3mm across. The thread is bound to be blown about by the wind, and because of its length it would be next to impossible to control the thread so that it fits into the tiny hole.
“Our only hope is to employ ‘eyes’ around the entrance to the borehole. In the Nankai Trough, we lowered an ROV [remotely operated vehicle] to the seafloor to monitor the area around the hole. The ROV carried aboard the CHIKYU can travel as deep as 3,000m, so this time we’re going to attach an underwater camera to a frame connected with optic and electric cables and lower it along with the drill pipe to ‘see’ what’s happening on the seafloor.”
If all goes well, the monitoring equipment off the Tohoku coast could shed new light on the mechanisms that triggered the world’s biggest earthquake and tsunami of this century.
■Miniature temperature logger (MTL) Measurement System
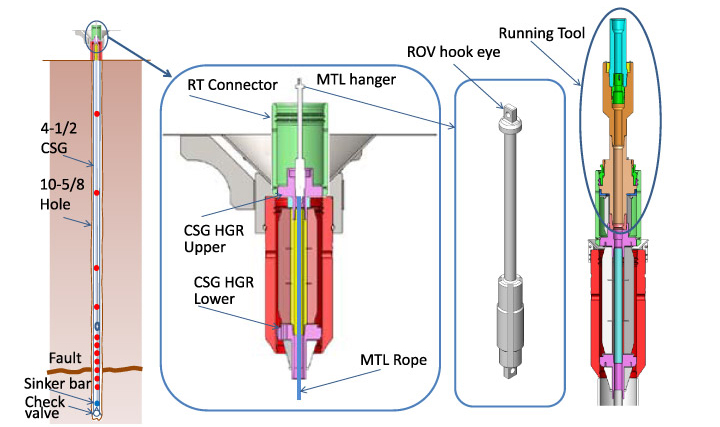
The first borehole, measuring 27cm across, will contain 55 heat sensors lowered inside a casing pipe with a diameter of 11cm. The sensors will be fitted onto a rope inside the pipe. A weight will be placed at the end of the rope so that it will remain straight inside the borehole. Sensors will be installed densely near the fault and sporadically higher up. The collected data will be recorded on a storage medium within each sensor. At the top end of the rope an “ROV hook eye” will be fixed to a device called the “wellhead” on the seafloor. Underwater imaging equipment—consisting of a camera, lights, and sonars—will be attached to a frame connected with optic and electric cables. This, too, will be lowered along with the drill pipe to “see” conditions on the seafloor. While the ROV takes images from the side, the underwater camera provide the view looking down. Operating from this angle will be a first for the CHIKYU and will present another major challenge for the crew.
■Weak Link
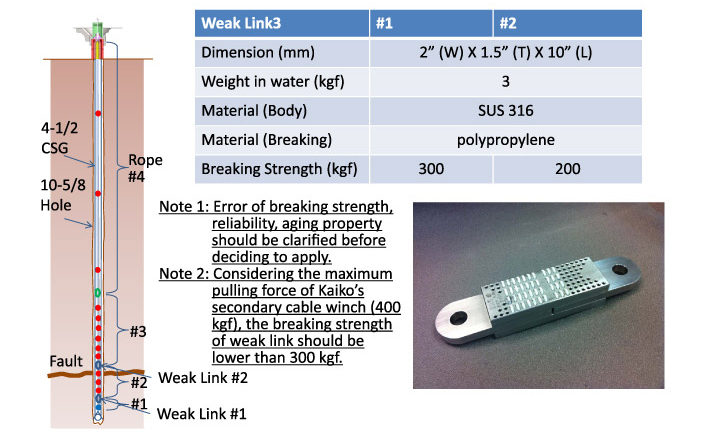
After an extended monitoring period, the sensors in the first borehole will be raised along with the rope. This will be performed by another ROV, the Kaiko II, which will be lowered to grab the hook at the top of the rope. Tectonic movements during the monitoring period could cause the borehole and casing pipe to deform, however. To avoid a situation in which the rope becomes stuck and cannot be raised at all, a “weak link” will be inserted beforehand where the rope can be split. This will enable at least the higher sensors to be raised.
■Pressure Monitoring System
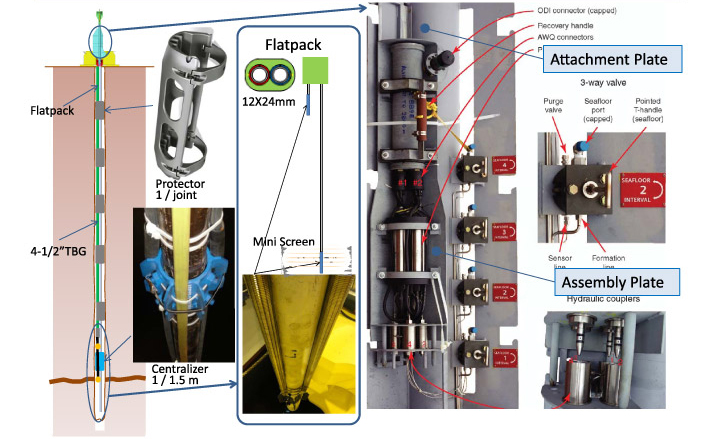
The second borehole will contain both heat and pressure sensors. While the heat sensors will, like the first borehole, be encased inside a pipe, the pressure sensors will be placed outside. They will be installed near the top of two oval-shaped transmission tubes measuring 12mm by 20mm that will hug the casing pipe and be surrounded by a protector. While each sensor in the first borehole will collect data separately, those in the second hole will send the data to a data logger on the ocean floor. An ROV is expected to be lowered to the floor to retrieve the logger, which will be fitted with an underwater quick-release connector. Other methods being considered are to either retrieve the logger itself or extract the data through acoustic transmissions.
- |1|
- 2|