The Tank Tests for the Arctic Research Vessel
November 14, 2022
Japan Marine United Corporation
Technical Research Center
Hydrodynamics Research Group
Ice Engineering Research Group
The Arctic Research Vessel (hereafter referred to as "the vessel") is an icebreaker capable of not only observing ice-free waters but also continuously breaking 1.2 m of first-year level ice at a speed of 3.0 knots (approx. 5.6km/h) to observe ice-covered waters. During the development stage, the ship hull shape and propulsion equipment are designed while evaluating the resistance and the power required for propulsion commonly through numerical analysis using computers. After the design phase of the vessel, performance was verified through tank tests using a manufactured high-precision scaled model ship.
This blog will introduce the tank tests conducted to verify the vessel's navigational performance in both ice-free waters and ice-covered waters.
The performance that must be verified includes propulsion performance in still waters and waves, navigation performance in ice-covered waters, stability in waves, seakeeping, dynamic positioning and maneuvering performance, and propeller cavitation. The series of performance verification tests were conducted from January to June 2022 using all four types of model basins (Towing Tank, Ice Tank, Seakeeping and Maneuvering Tank and Cavitation Tunnel) at Technical Research Center of Japan Marine United Corporation. The tests were conducted using model ships of sizes appropriate for the size of each tank and the test conditions.
(Note) Propeller cavitation: When a propeller rotates over a certain speed, vapor bubbles are generated from the propeller blade surfaces and tips with a significant change of water pressure, and which is called the cavitation phenomenon. It may result in damage to the propellers and rudder (erosion), and cause serious adverse effects on the hull vibration and noise. Since the vessel will have underwater acoustic measurement equipment, the shipbuilder and the manufacturer carried out various kinds of tests and optimized the shape of the propeller blade using the test results to be free from harmful cavitation which may impact on observation operations.
In this test, a scaled model propeller (the same shape as adopted on an actual ship) is rotated in a circulating water tunnel under the reproduced same condition as the actual operation to observe the occurrence of cavitation.
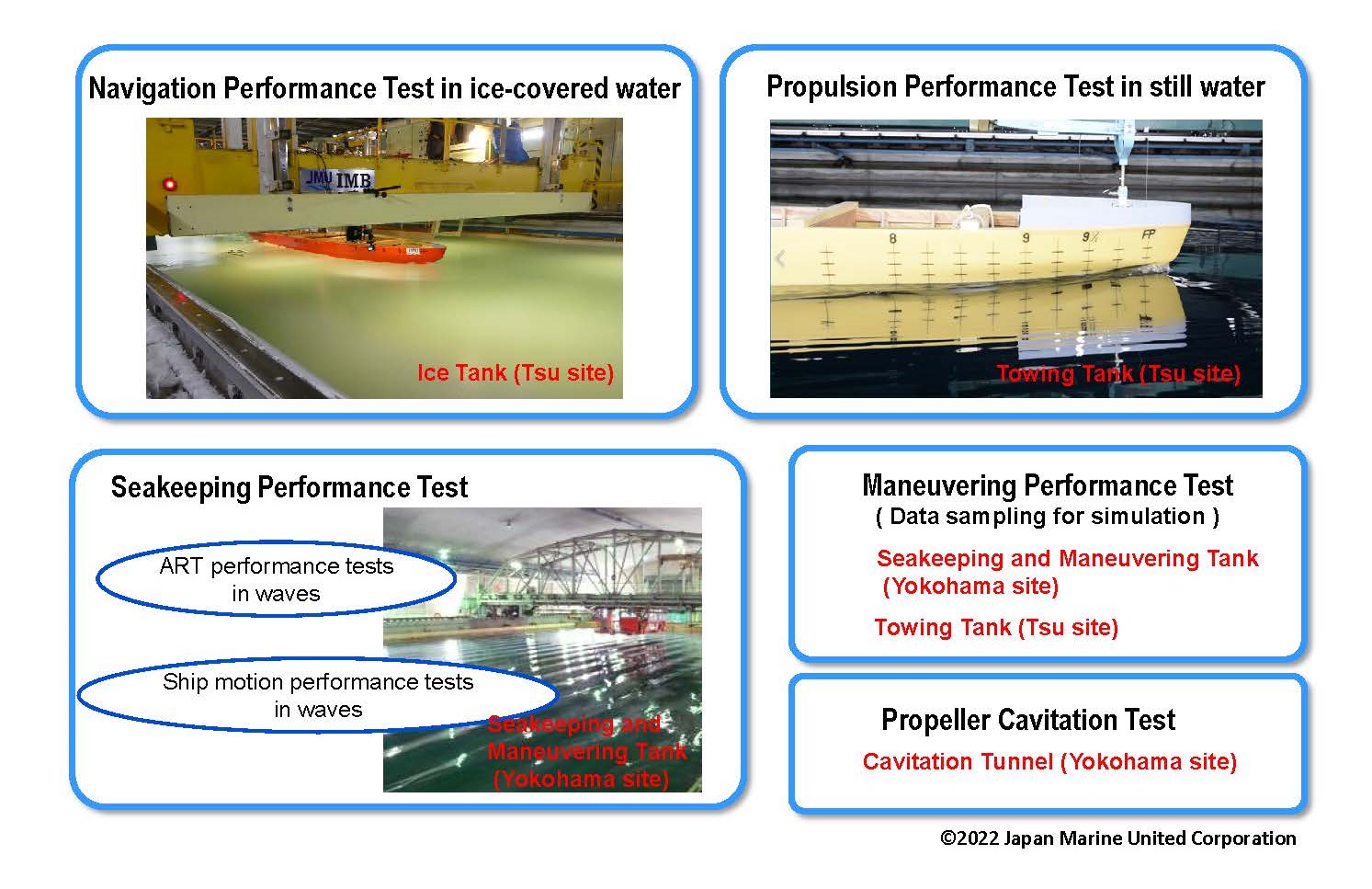
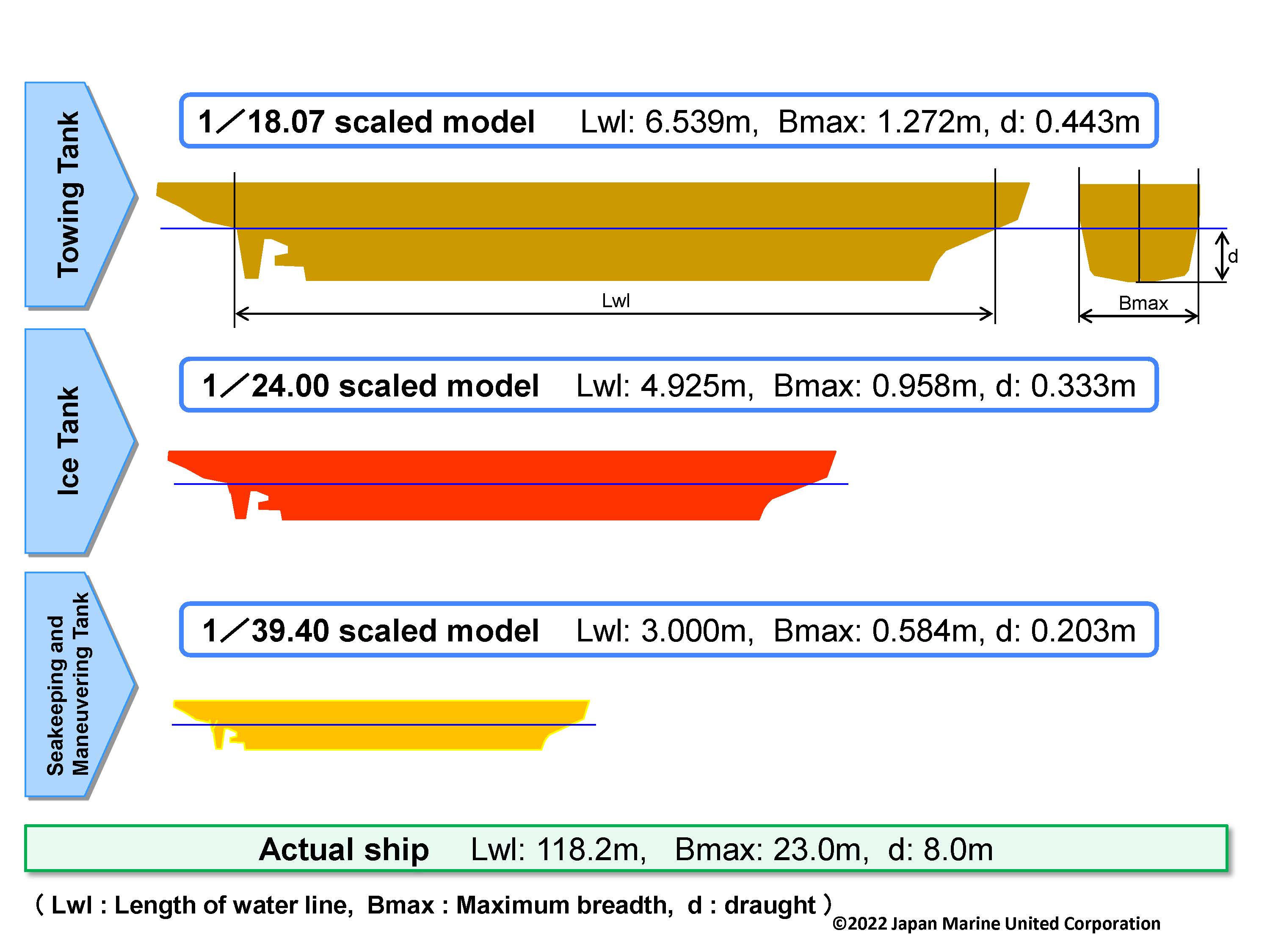
Propulsion Performance Test in still water
Propulsion performance in still water (no wave states) is fundamental in evaluating the performance of icebreakers in ice-free seas (open water). Icebreakers generally tend to have inferior performance to normal ships in still water due to the distinctive shape of their bow and other parts that make it easier to break ice floes.
The resistance tests and the self-propulsion tests in still water are conducted in the towing tank, and the results of these tests help us to estimate the relation between the power required for propulsion and the ship's speed (power curve). The results from the tank tests proved that the planned performance in still water was satisfactory. The power required for the propulsion system at cruising speed is equivalent to that of R/V Mirai which is a little bit smaller ice-strengthened oceanographic research vessel.
The waves generated as the vessel moves forward affect propulsion performance and underwater observations. However, we have confirmed that the waves generated by the vessel are kept small for an icebreaker.
(Note) Resistance test: Towing the model ship to examine the resistance of the ship.
(Note) Self-propulsion test: Towing the model ship while activating the propeller to measure resistance and propulsive force simultaneously, and examine the efficiency required for power estimation.
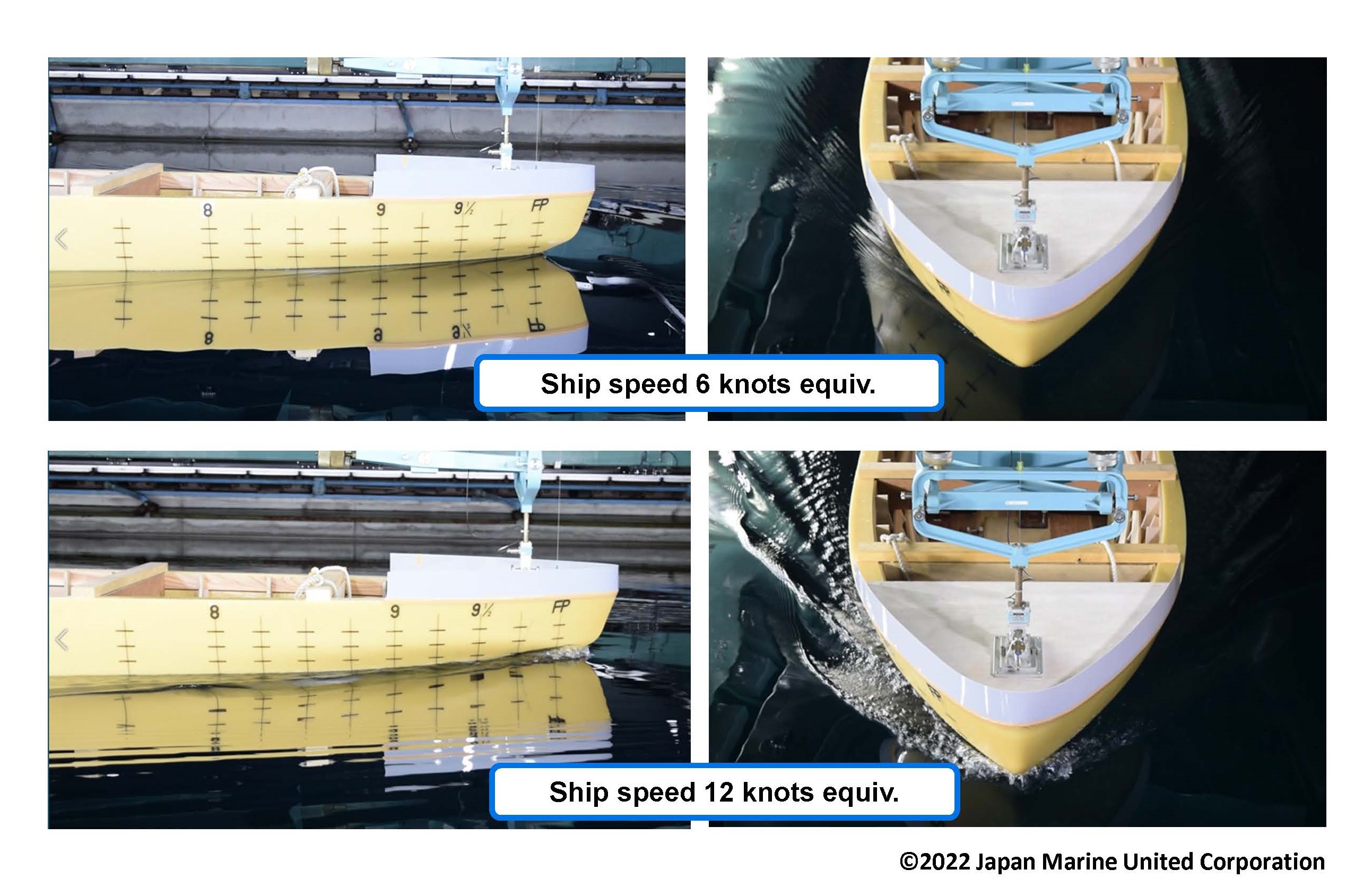
Navigation Performance Test in ice-covered water
To verify the ice-breaking capability of the vessel, continuous ice-breaking tests (including resistance and self-propulsion tests) in level ice (ice of constant thickness over a wide area) were conducted in the ice tank. Based on these results, the interrelationship between level ice thickness, ship speed, and propulsion power was estimated. The vessel was confirmed to be capable of continuously breaking 1.2m thick level ice at the speed of 3 knots as planned. Propulsive efficiency deteriorates when ice fragments flow across the ship's bottom and interfere with the propellers after the ice breaking. However, the ship's shape design to minimize the interference of ice pieces with the propeller was effective.
- VIDEO <Resistance test in level ice (Movie above level ice) >
- VIDEO <Resistance test in level ice (Underwater movie) >
When the vessel encounters a heavy ice condition, such as thick multi-year ice (ice that survived one year's melt), the icebreaker goes backward and then accelerates ahead to break through sea ice by hitting the ice sheet with its hull. This is called ramming.
The ramming test was also conducted in thick level ice during the ice tank test to evaluate the capable break-through distance with the ice in a single ramming. Other tests included a resistance test in ice floes to estimate the resistance and required propulsive power when navigating in pack ice conditions, and an initial turning test in level ice estimating the turning diameter in level ice.
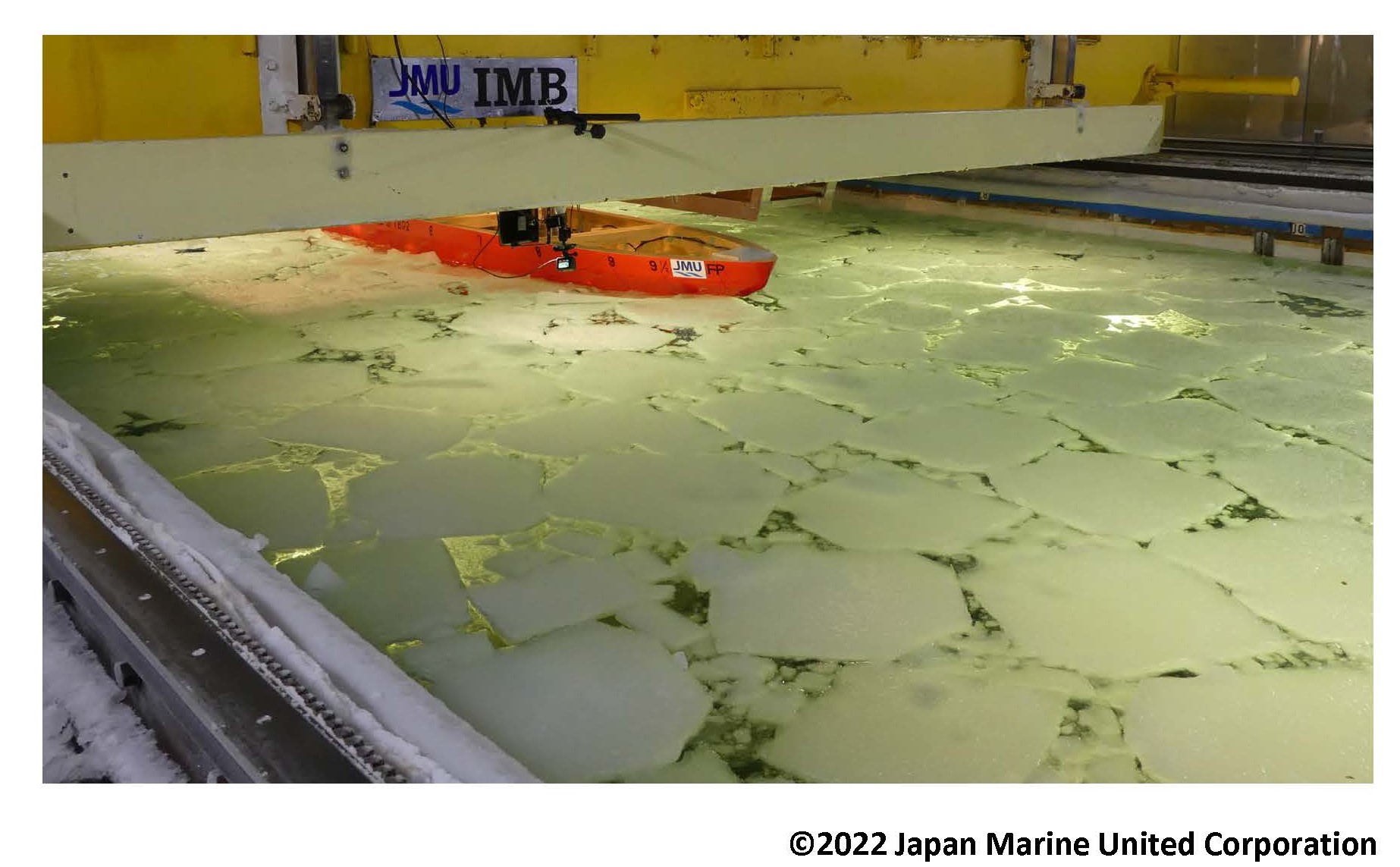
- VIDEO <Initial turning test in level ice (Ice thickness: 0.8m, Ship speed:4.7knots equiv.)>
Seakeeping Performance Test
When the natural period of rolling motion and the period of waves come to a close, the rolling motion of the ship increases in amplitude. To reduce rolling motion, the vessel will have an Anti-Rolling-Tank (ART) by moving the liquid in the U-shaped tank on board in the opposite direction to the ship's tilt. The rolling motion test of the vessel was conducted both with and without ART installed condition in the beam waves (regular and irregular waves) at the Seakeeping and Maneuvering Tank to confirm the performance of the ART.
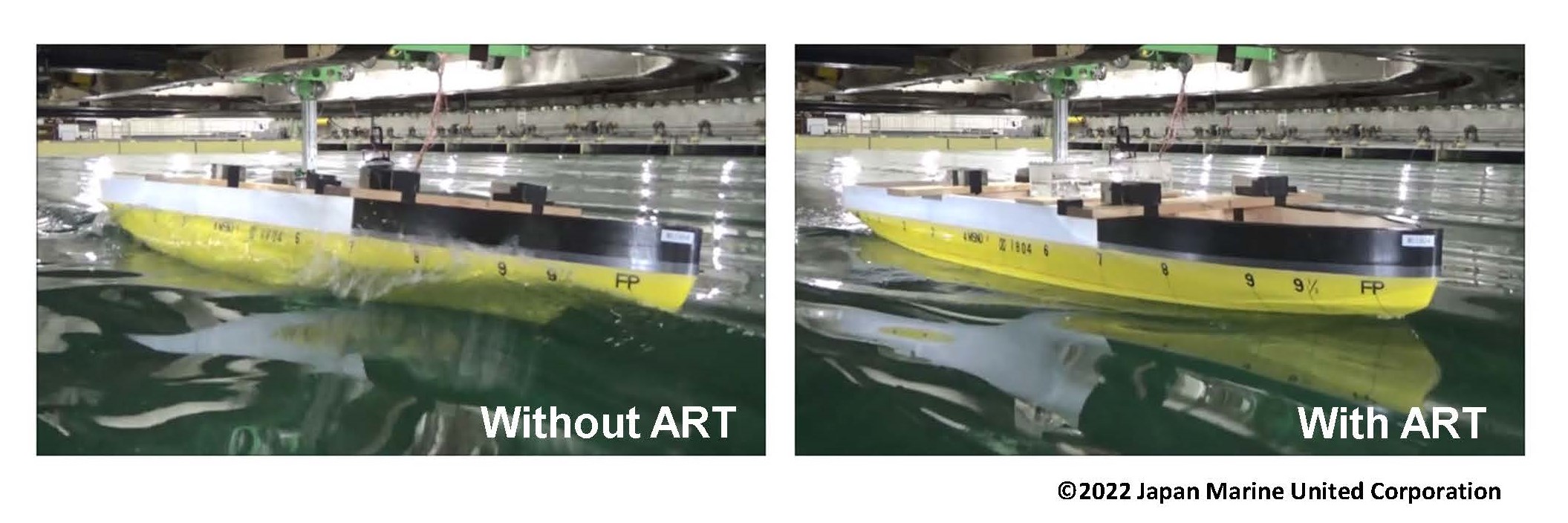
- VIDEO <Roll motion test in regular beam wave without ART>
- VIDEO < Roll motion test in regular beam wave with ART>
With ART on board, tests were conducted under various conditions with different wave directions as well as beam waves to estimate the response characteristics of added resistance and ship motions to wave directions and periods. Based on these response characteristics, it is possible to predict the resistance increase and ship motion in actual sea conditions (where various waves are superimposed.)
We also estimated the relation between the speed and propulsion power of the vessel in waves (power curve) under assumed sea conditions with the results of the predicted added resistance in waves and the analysis of the propulsion performance test in still water.
Maneuvering Performance Test
For a certain type of ocean observation, it is important to maintain the ship's position surrounded by an environment with waves, wind, and ocean currents. The vessel is designed to be able to hold its position within a radius of 60 meters in the presence of wind speeds of 15 m/sec, significant wave heights of 3 meters (wave direction and wind direction are in the same direction), and currents of 5 knots from a direction within 30 degrees of the vessel's bow. The vessel has three thrusters in addition to the propulsion system and rudder at the stern, which is necessary for normal maneuvering, in order to maneuver to maintain its position.
Since it is difficult to accurately reproduce the actual ship's movement in a model basin where waves, wind, and currents act simultaneously and the actual ship's movement, the performance of the vessel to hold its position is verified by simulation.
Maneuvering performance tests were conducted in the Towing Tank and Seakeeping and Maneuvering Tank to determine the forces acting on the hull, rudder, and propeller during maneuvering and their interaction effects as maneuvering hydrodynamic coefficients, which are necessary for simulation calculations.
As a result, we have confirmed that the vessel has the designated performance to hold its position.
- VIDEO < Steady circular test - measurement of rudder force and propeller thrust (Landscape) >
Propeller Cavitation Test
Depending on operating conditions (speed, rpm, and draft), propellers sometimes generate cavitation that can cause propeller blade damage (erosion) and loss of thrust. Since the vessel will have underwater acoustic measurement equipment, it is designed to be free from harmful cavitation which may impact on observation operation. A scaled model propeller (the same shape as adopted on an actual ship) is rotated in a circulating water tunnel under the reproduced condition as the actual operation at the stern to observe the occurrence of cavitation.
Cavitation was observed in some of the test conditions, but they were not harmful. The propellers are performing as planned not only in terms of propulsive performance but also in terms of cavitation suppression.
- VIDEO < Model propellers cavitation test Normal blade angle, at a speed of 12 kt >
- VIDEO < Model propellers cavitation test Normal blade angle, with MCO >
- VIDEO < Model propellers cavitation test Blade angle for ice-covered waters, during the continuous ice-breaking state in 1.2m thick level ice at 3kt >
In conclusion,
It is impossible to predict and incorporate into the tank tests all of the sea and ice conditions that the vessel would encounter. However, we believe that we were able to confirm the fundamental performance of the plan through the series of tank tests.